
Tailored compositions and functional grading in deposited layers are possible by using the multi-material MELD™ feeding system. MELD™ machines are capable of processing a variety of raw material forms, including solid bar, powder, granules, pellets, beads, flakes, and even scrap pieces generated from subtractive operations. MELD is even capable of fabricating components or repairs using unweldable metals. Materials used to date include magnesium, aluminum, aluminum silicon carbide, copper, copper metal matrix composites with a wide variety of refractories, magnesium, steel, oxide dispersion strengthened steel, ultra-high strength steel, nickel-based super alloys, titanium, and more. All of this is possible with one machine that can process a broad spectrum of materials including, but not limited to, metals, composites, and their combinations. New MELD™ machines offer a novel, environmentally-friendly, scalable, method to perform a range of solid-state deposition processes, including coating of dissimilar materials, building 3D structures, creation of new alloys and customized compositions, repairing, and joining. Further, it yields properties that are near, at, or exceed wrought, at high deposition rates. With a new commercially available machine, users can do more than additive manufacturing, with multiple materials, in open atmosphere. Its flexibility for material inputs and for process uses is unmatched. The patented MELD™ process is innovative because it is the first non-melt-based process to make metal and metallic parts at large scale in the industry. This is the future of additive manufacturing at scale. Because it can be scaled to manufacture very large parts, it will open up new possibilities for the use of additive manufacturing at sizes never before seen. This patented process is unique and differs from others because there is no melting of the metal.
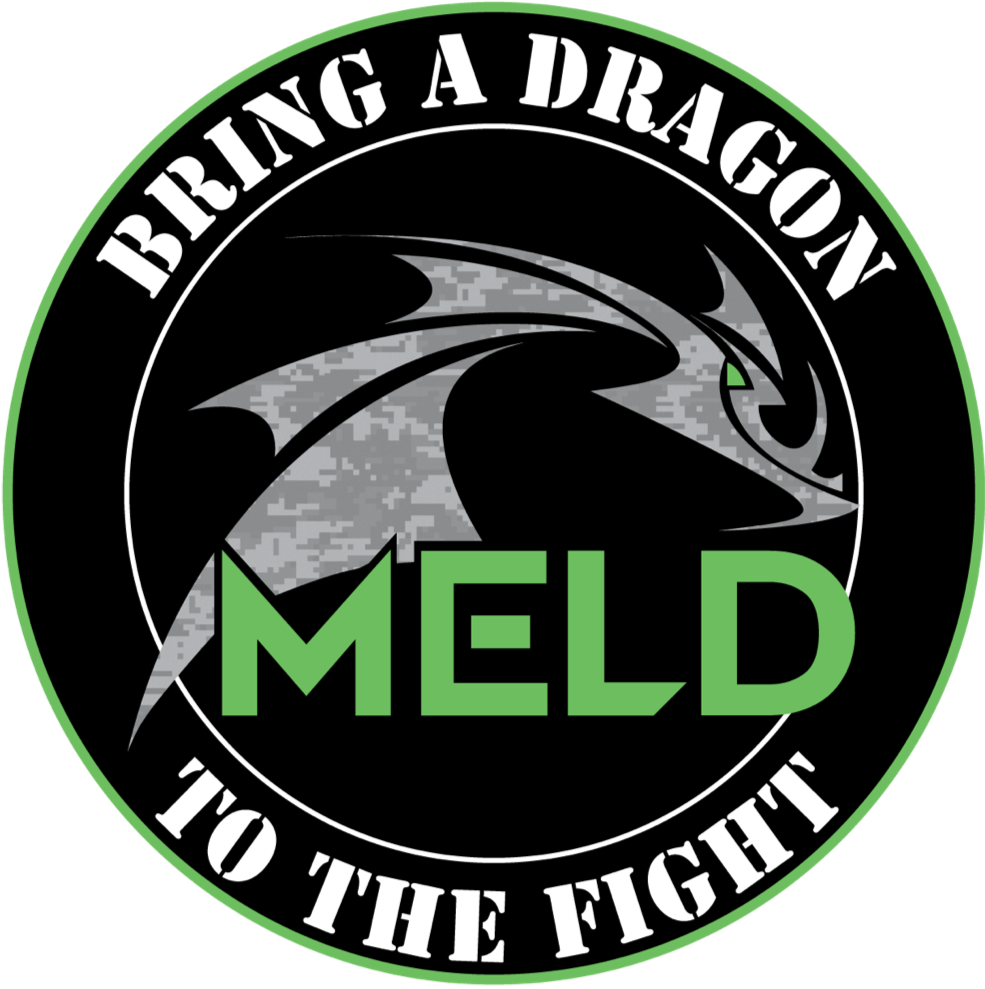

Our mission is to revolutionize manufacturing across industries with our innovative technology for additive manufacturing, or 3D printing, of metals.
